Among the main features are:
- Freedom for choosing hardware suppliers: You can select from different PLC vendors and still keep all the features of an integrated solution.
- Development Standardization: By using a model based on a standardized philosophy, you can maintain implementation quality between different teams and professionals.
- Shorter configuration and maintenance time: This time is reduced due to ready-to-use interfaces and models.
- Shorter downtime: With better diagnosis tools, engineering and maintenance teams can, if necessary, adapt the system more rapidly and find possible solutions for the plant more easily.
- Better system quality for the end-user: Standardization allows investing in ready-to-use interfaces, libraries, and reports that add great value to the solution, when compared to traditional SCADA systems where such features had to be developed individually for each application.
- Increased profitability for systems integrators: Using a robust, flexible standard for all clients allows systems integrators to minimize costs with development and technical support. Additionally, different staff members can be allocated to any project at any time, and work with maintaining and developing different systems with no previous knowledge about any particular projects.
Architecture
Elipse FlexControl DCS offers a groundbreaking platform for developing an automation system; it does so by adding an abstraction layer to set up the process between the supervisory system and the controller.
This tool allows defining and giving meaning to the main entities in a system. This configuration, in turn, is followed automatically by a data model inside the supervisory, which is then automatically bound to the same entities declared in the process controller. FlexControl DCS’s editor is accessed from any console in the operation.
Because it is based on Elipse E3 and other Elipse products, FlexControl DCS inherits all benefits from a robust, highly flexible solution.
- Uses either virtual environment or physical machines.
- Support to servers redundancy, with splitting and sharing of load between pairs (domains), according to the application size.
- Electric system fully integrated to the process, which allows operating both from the same system. Elipse Power provides connection to any type of equipment via native drivers and intelligent modules, such as load discharge, oscillograph collection, status estimators and operators training tools, in addition to the operation of electric power generation, transmission, and distribution.
- Alarms management work according to standard ISA 18.02 and EEMUA, through native features, reports, and actions suggested by Elipse Alarm Manager (EAM).
- Historic and intelligence tool on all the data from the process, provided by the integration with Elipse Plant Manager (EPM). Among the actions offered by EPM are:
- Add-in for Microsoft Excel;
- OPC UA Server;
- Dashboards Portal;
- Powerful calculation tool via Python language;
- Trend chart tools, with integrated calculation (Python) and notes;
- Integration with Microsoft Reporting Services.
User profiles
Elipse FlexControl DCS was developed for different the user profiles commonly found in industrial plants:
- Integration Engineers: Responsible for the system’s architecture and modeling.
- Process Engineers: Changes in the process, equipment replacement, or other occurrences can force them to modify system logic or instructions for the operation.
- Operators: Need to keep the system stable and be warned with intelligence about issues.
- Maintenance Technicians: Need to retrieve reliable, quick information about issues in the equipment or in processes in order to prevent stops or make them shorter.
- Process Managers: Attentive to the plant’s productivity and science, these professionals strive to improve this process. Need to be alerted on any major issues.
Tools
- FlexControl DCS Editor: Tool where the main entities in the system are defined, in high level. It offers diagnosis and allows changing the meaning of variables, which can be applied automatically in the production environment.
- Controller Programming: Offered by the controller’s vendor, it allows setting up the operational logic or the rule of the process which are specific for each entity.
- E3 Studio: Sets up all other entities in the system, operation interfaces, and synoptics to be used by the operator.
- E3 Viewer: System’s operational and visualization interface.
- EPM: Historian and analysis tool, it provides statistics and reports on the system’s performance and behavior, in order to facilitate plans for corrective actions and improvements in the process.
- EAM (Optional): Collects the history of alarms and events generated by the system. Via a web interface, offers a series of reports and suggests actions for the operation environment.
- Elipse Mobile (Optional): Allows the user to interact with the plant from anywhere; they can: view the conditions of the process, exchange messages, collect data, or even send commands with safety control and permissions.
FlexControl Entities
Elipse FlexControl DCS offers a robust standard for developing applications, based on a set of configurable entities:
- PLC: Stands for a process controller supported by the system, which is responsible for a certain area in the process. The system can support hundreds of controllers, oftentimes split into redundant pais called domains, according to the desired architecture. Currently, the system comprises the following controllers (but allowing for the addition of new ones, according to demand or by adapting pre-existing ones):
- Rockwell ControlLogix;
- Siemens S7-300, S7-400, 1200, 1500;
- GE PAC, Rx3i, Rx7i;
- Schneider Premium, Quantum;
- Altus Nexto.
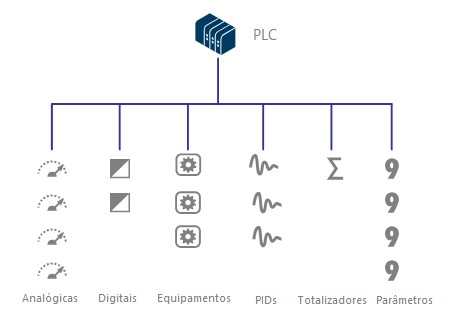
- Analog: Analog variables in the process, with filter and alarms configurations carried out both by the controller and the system, independently;
- Parameters: Setpoints or configuration analog parameters;
- Equipment: Data structure that stands for a device to be controlled, a subsystem, or a component. This is defined in the engineering stage, according to each device’s degree of relevance. The equipment structure contains the definition of other properties as well:
- Digital: Grouping of discrete signals and their meanings;
- Commands: Definition of actions and their respective authorizations and interlocks;
- Defects, interlocks, alerts, permissions: Conditions for starting, stopping, functioning, protections, and warnings;
- Hobbs meter: Time measurement on or off;
- Analog and parameters: List of associated variables to be displayed at the operation’s faceplate;
- PID: PID controls related to the process’s mesh;
- Totalizers: Their goal is to continuously integrate the analog values, usually represented by the measurement of its material outflow. Via totalization, different production or expenditure reports can be generated by the hour, month, day, or shift, among others;
- Digital: Digital variables that fit no specific device, such as system items or general instructions.
Modelling
The outcome of editing entities (register interface) generates a process data model that is automatically connected to the system’s I/O driver. Tags are created remotely in the communication interface (driver).
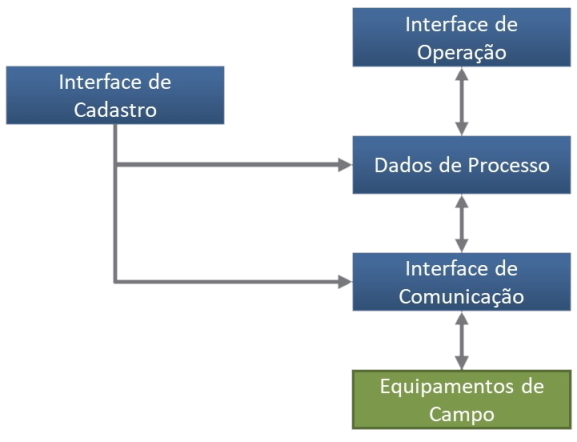
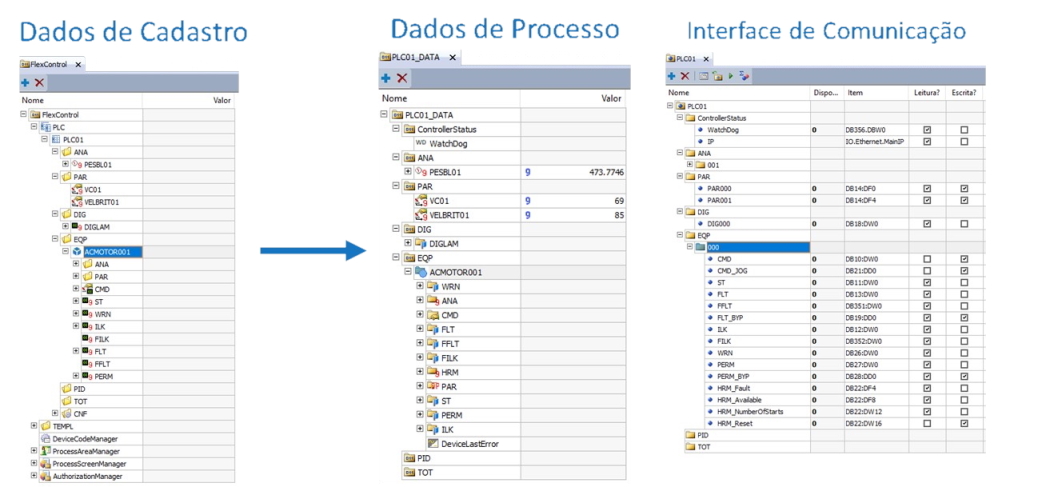
Control Objects Libraries
Elipse Flex Control DCS offers libraries made of the typical objects for each of the supported controllers, standing for the data transfer area between FlexControl DCS and each entity, as well as for the implementation of the control block.
The user programming the controller must set up the areas where data switch will take place according to the definition of typical objects and add the process logic from each of these objects.
Benefits
- Robustness and reliability;
- Communication capacity and versatility;
- Servers redundancy and distribution;
- Support to virtualization;
- Adherence to any type of continuous process: mining, steelwork, oil, gas, chemical industries, paper, cellulose, sugar, alcohol, agribusiness, and wastewater;
- Freedom for choosing hardware suppliers;
- Developed for reducing developmental costs;
- Shorter configuration and maintenance time;
- Better system quality for the end-user.